Stress Corrosion Cracking (SCC) is a cracking phenomenon that is crucial to consider when working with specialty alloys.
SCC is often associated with chlorides but can also occur with exposure to caustic and other corrosive media. The most common type of stress corrosion cracking in stainless steels occurs in chloride environments, which will be the focus of this discussion.
Three underlying factors must be present to cause SCC:
1) Stress
2) Aqueous Corrosive Media
3) Elevated Temperature
Stress could be from an external source, such as a pressurized vessel, or an internal source, such as a weldment containing residual stresses. Temperatures typically need to be higher than 120°F for SCC to occur in stainless steel. Under certain conditions, SCC can occur at much lower temperatures.
When we consider chloride-induced SCC in specialty alloys, the nickel content is one of the primary indicators of an alloy’s susceptibility. Below is a diagram called the Copson Curve, which plots an alloy’s nickel content on the x-axis and the probability of succumbing to SCC on the y-axis. This diagram shows that the more nickel in an alloy’s composition, the less susceptible it is to SCC. Additionally, on the far left of the Copson Curve, in the region of alloys containing little nickel, ferritic stainless steels and duplex stainless steels are shown to be far less susceptible to SCC than austenitic stainless steels. The reason for this is the ferrite in their microstructure. Ferrite effectively pins SCC before it can propagate into the base material.
AL-6XN®, with only 25% nickel, appear susceptible to SCC based on plotting the alloy on the Copson Curve. In actuality, AL-6XN offers good resistance to SCC. Reasoning for this is its molybdenum content. Like nickel, a higher molybdenum content increases an alloy’s resistance to SCC.
Another way to look at an alloy’s performance to SCC is to consider the threshold temperature at which SCC begins. The below figure shows threshold temperatures for some alloys when exposed to a 5% sodium chloride solution.
Generally, 316/316L should not be used when chloride concentrations exceed 1,000 ppm. In non-acidic environments, 2205 can tolerate chloride levels as high as 8,000 – 10,000 ppm. Super duplex materials, such as Zeron® 100 and 2507, and super austenitic alloys like AL-6XN®, can be used in environments containing up to 50,000 ppm chlorides. Super duplex and super austenitic stainless steels are considered virtually immune to chloride stress cracking.
One note of caution: Chlorides can become easily concentrated. Chloride concentration will rapidly increase when the solvent liquid can evaporate. A few hundred ppm of chlorides can increase to several thousand. A few thousand ppm of chlorides can increase to several tens of thousands. When measuring chlorides, measure those in the system as it operates, not the concentration in the incoming fluids.
The following are macro and micro examples of typical SCC appearance.
Please contact the Rolled Alloys Metallurgical Services group at 1-800-521-0332 or email us metallurgical-help@rolledalloys.com if you have additional questions.
Buy Online Anytime
Our dashboard makes it even easier to shop online anytime from anywhere. Quote, buy, and track 24 hours a day at rolledalloys.com.
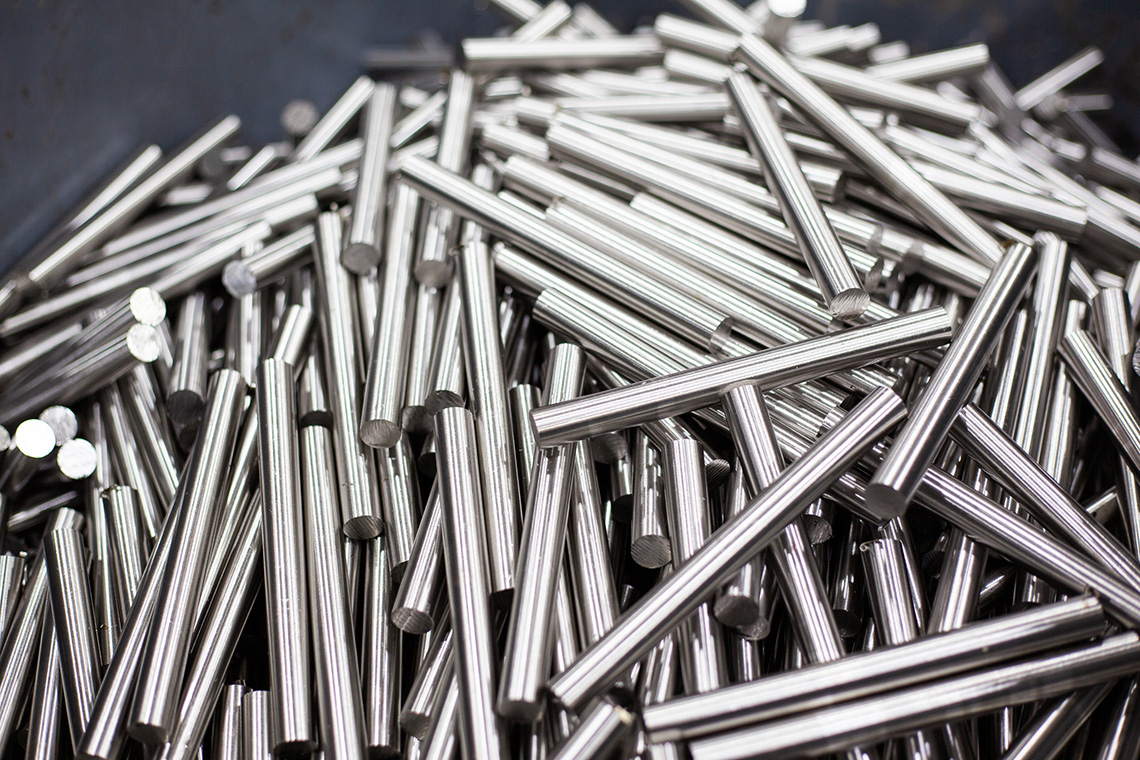
Cut to Size Processing
We offer a range of processing services to provide material ready for you to begin machining or fabricating upon arrival.
See our full list of capabilities for tolerances or chat with a sales rep about which processing method would be best suited for your order.

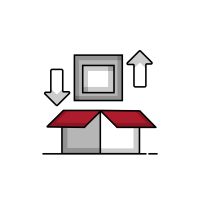
Stocking Programs
Our e-service stocking programs put you in the driver seat by using our customized purchasing options to order your recurring material with ease.
Whether you have an internal process for purchasing and receiving in place or maybe looking for solutions to become more efficient, we have a program that will work for you.
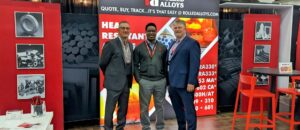
Trade Shows
Come talk to a Rolled Alloys representative in person about your project. You can find us at these trade shows.
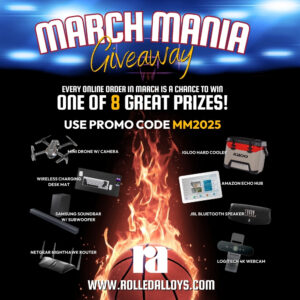
March Mania 2025
Every Online Order in March is a Chance to Win One of 8 Great Prizes!
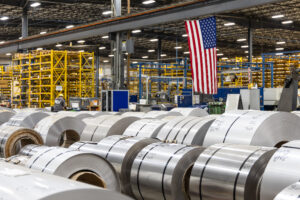
Instant Pricing on Nickel, Stainless Steel, Duplex, and Titanium
Get real-time pricing and availability for nickel, stainless steel, duplex, and titanium—all in one place.
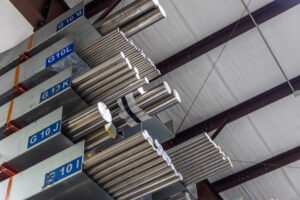
New and Expanded Stock for 2025
New Titanium, Stainless, Nickel and Cobalt in Stock Now – CP Ti Grade 2, 635, 718 and More!
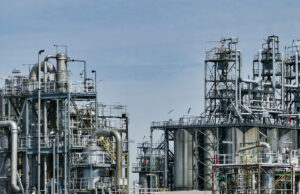
History and Uses of Alloy 800
Discover the evolution of Alloy 800, from its origins during the 1950s to modern derivatives like Alloy 800H/800HT. Learn about its high-temperature strength, petrochemical applications, and commercial availability today.
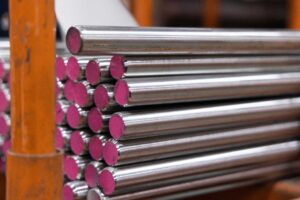
New Bar Stock Available
New Round and Flat Bar Products in Stock at Rolled Alloys