The Evolution of Alloy 800
Alloy 800 is a grade that has undergone significant changes over time, resulting in various derivatives. Since its introduction, it has been extensively utilized in the petrochemical and refining industries, particularly in applications requiring high strength at elevated temperatures. This guide provides an overview of the historical development of alloy 800, industrial applications, and current commercial availability.
Origins and Development
There are several distinct versions of alloy 800, which have evolved due to changes in alloying and grain size requirements, primarily driven by a means of enhancing the alloy properties. Understanding these variations is crucial when selecting the appropriate grade of 800 for an application.
The original alloy 800 was developed by Inco Alloys, now Special Metals Corporation, in the 1950s. It was created to meet the demand for a heat-resistant alloy with low nickel content, a necessity brought on by the nickel shortage during the Korean War. Before the introduction of alloy 800, the most commonly used heat-resistant alloy was alloy 600, which contained approximately 76% nickel in its composition.
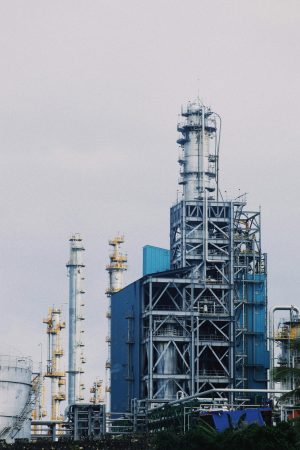
Originally, alloy 800 was offered in two grades: Grade 1 and Grade 2. Grade 1 had a fine grain size and was typically annealed at approximately 1800°F. In contrast, Grade 2 underwent solution annealing at approximately 2100°F. This higher-temperature annealing process resulted in coarser grain sizes, which enhanced the alloy’s creep strength.
In the early 1970s, Grade 2 evolved into alloy 800H, establishing a minimum carbon content of 0.05% and a grain size requirement of ASTM 5 or coarser. During the 1980s, in an effort to enhance creep strength and obtain higher ASME allowable design stresses, the carbon content was adjusted to a range of 0.06% to 0.10%, the minimum for aluminum and titanium content were increased to 0.25%, and an aluminum plus titanium content requirement was established. As a result of these changes, Inco introduced this new grade as 800HT®.
After the patent for 800HT expired, other nickel alloy manufacturers began producing 800AT, a generic version of 800HT that shares the exact Unified Numbering System (UNS) designation.
Current Industrial Use
800H/AT is a high-strength alloy commonly used in the petrochemical and refining industries for various furnace components, including furnace cracker tubes, pigtails, calciners, and other equipment requiring high creep strength. Today, 800H/AT has one of the highest creep strengths among wrought alloys and some of the highest ASME allowable design stresses for a heat-resistant wrought alloy. This alloy achieves its strength through a combination of factors that include:
- Coarse grain size resulting from a minimum solution annealing temperature of 2100°F.
- High carbon content ranging from 0.06% to 0.10%.
- Total aluminum and titanium content of 0.85% to 1.20%.
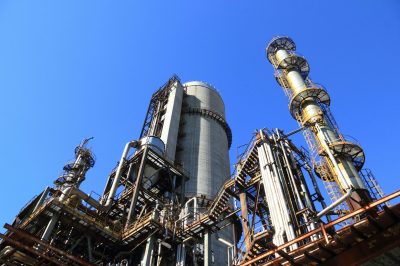
Due to its coarse grain size, 800H/AT exhibits excellent creep resistance. However, it tends to have poor resistance to thermal shock and thermal cycling. As a result, 800H/AT is primarily used in high-temperature applications where the temperature does not fluctuate significantly in a cyclic manner.
In addition to its poor thermal cyclic resistance, 800H/AT is highly susceptible to stress relaxation cracking (SRC). This vulnerability is due to its coarse grain size and the presence of fine strengthening precipitates. Based on API 942-B, the best prevention against SRC is to perform a post-weld heat treatment (PWHT) at a minimum temperature of 1625°F for 1.5 hours before a fabrication is put into service. Consequently, pressure vessels designed according to ASME Code made from Alloy 800H and/or 800HT/AT must undergo PWHT if they are to operate at temperatures exceeding 1000°F.
Commercial Availability
Today, most alloy 800 is dual certified as 800H/800AT or 800H/800HT. It is rare to find alloy 800 straight grade available in a quantity lower than that of a heat lot.
Comparison of Different Versions of Alloy 800
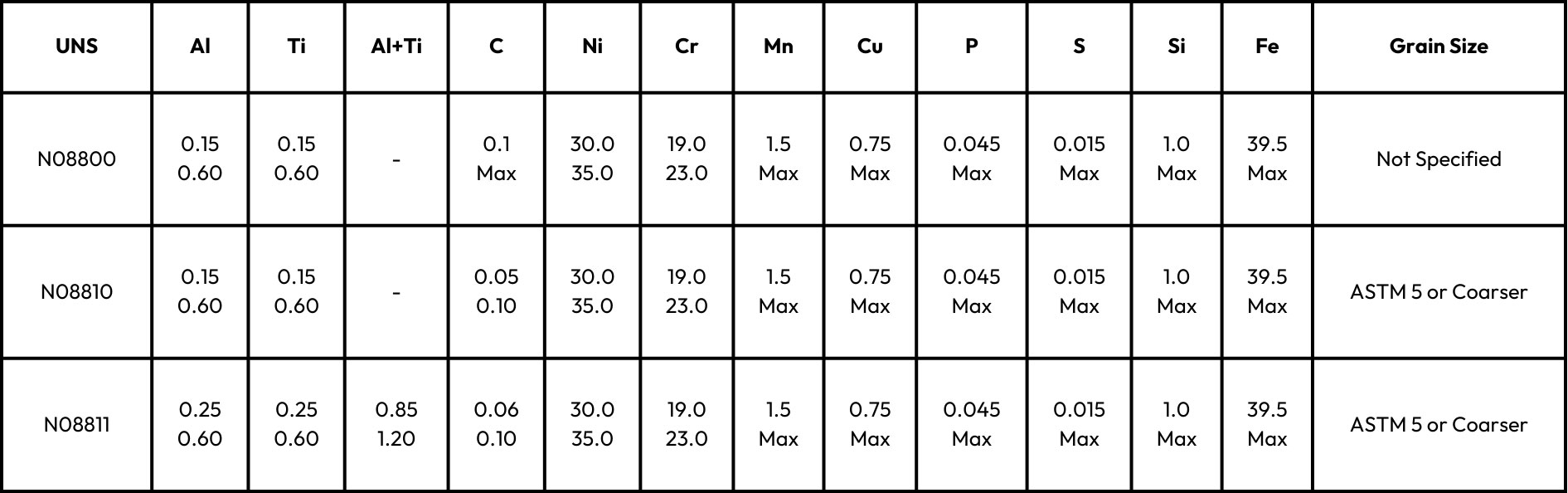
References
(2004). The story of the “INCOLOY® alloys series,” from 800, through 800H, 800HT®. Special Metals. https://doi.org/Publication Number SMC-047
Buy Online Anytime
Our dashboard makes it even easier to shop online anytime from anywhere. Quote, buy, and track 24 hours a day.
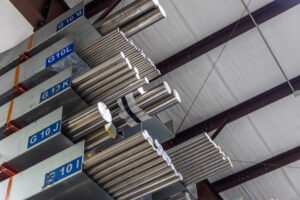
New and Expanded Stock for 2025
New Titanium, Stainless, Nickel and Cobalt in Stock Now – CP Ti Grade 2, 635, 718 and More!
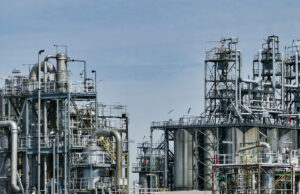
History and Uses of Alloy 800
Discover the evolution of Alloy 800, from its origins during the 1950s to modern derivatives like Alloy 800H/800HT. Learn about its high-temperature strength, petrochemical applications, and commercial availability today.
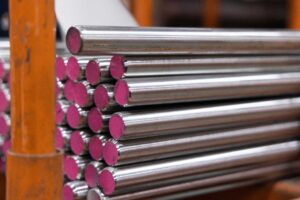
New Bar Stock Available
New Round and Flat Bar Products in Stock at Rolled Alloys
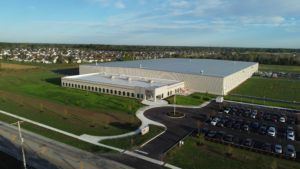
New Rolled Alloys Facility in Ohio
Rolled Alloys announces new facility located in Toledo, Ohio.
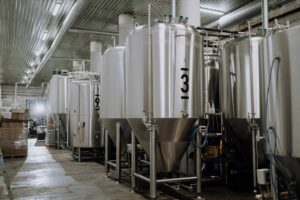
Reasons Why Duplex Stainless Steels are Replacing the 300 Series
Explore the four key benefits of duplex stainless steel: high strength, superior corrosion resistance, ease of fabrication, and cost-effectiveness. Understand why 2205 is favored over 304/304L and 316/316L for industrial applications.
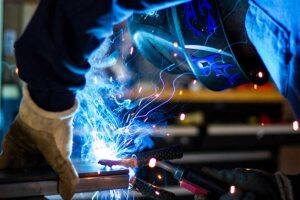
Understanding P-Numbers and F-Numbers in Welding
P-Numbers and F-Numbers are essential classifications in the welding industry, particularly for projects that follow ASME codes and…