PRODEC® ENHANCED MACHINING GRADE
PRODEC® (PRODuction EConomy) bar products are used to increase productivity and efficiency by enabling the use of high speeds and feeds with less tool wear. PRODEC® bar meets all standard ASTM, AMS, ASME and QQ-S specifications, while carefully controlled chemistries and physical properties ensure consistent quality.
The manufacturing process of PRODEC® bar allows for high quality machining from heat to heat. With strict limits on the chemical and physical properties, the PRODEC® manufacturing process also controls the composition, size, shape and distribution of the non-metallic inclusions so that they are favorable to machining operations. Oxide inclusions are no longer the primary cause of tool dulling, and under the right conditions they can provide lubrication between the tool and chip. The tool will last longer even under extreme machining conditions. PRODEC® bar products are available in 303, 304/304L, 316/316L and 17-4.
Machining Standards
Austenitic stainless steels can be difficult to machine because:
- These steels are relatively poor conductors of heat, which means that cutting produces localized temperature increases.
- Common deoxidation practice leaves behind inclusions capable of dulling even cemented carbide tooling.
- Austenitic stainless steels undergo strain hardening if mechanically deformed.
- When your tool is dulled by hard inclusions, it pushes the austenitic stainless steel rather than cutting it, forming an extremely hard surface layer.
- The high hardness of austenitic stainless steels make for tough cutting and poor chip- life.
- The material tends to stick to the tool, producing a built- up edge and aggravating tool wear.
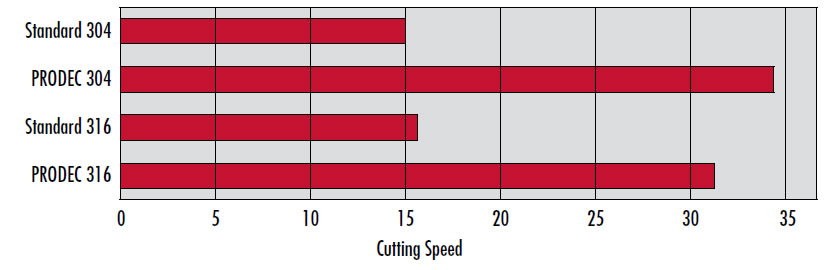
Machining Practices
Using correct cutting processes can save time and money. Whether it is “common stainless” or PRODEC® quality, there are certain machining practices that should always be used with stainless steels.
Machining practices for austenitic stainless steels:
- The machine should be rigid, and the tool and work piece should be rigidly mounted.
- Vibration is highly detrimental to tool life.
- A large nose radius of the tool should be avoided to minimize vibration.
- Use tools that will retain sharpness. The tools should have a large positive rake, with an edge chamfer that provides a true cutting edge without excessive weakening of the cutting edge.
- Use sufficient cutting depth to ensure penetration below the hardened zone caused by the previous cuts.
- Replace or re-sharpen tools on a regular basis before they become dull and cause surface hardening.
- Use adequate lubricants such as oils or emulsions with EP additives, to facilitate heat removal.
- Use the correct cutting speed. Speeds too low will produce build-up edges, while speeds too high will produce excessive tool wear.
PRODEC® 303 is a fully resulfurized free-machining austenitic stainless steel melted and processed to maximize machinability. It should be considered for automatic screw machines where extensive machining is required. PRODEC® 303 is nonmagnetic in the annealed condition, but may become slightly magnetic as a result of cold working.
PRODEC® 303 is resistant to mildly corrosive atmospheres, but is inferior to 304 because of the high sulfur content. For optimum corrosion resistance, it is recommended that PRODEC® 303 be chemically treated to remove sulfides from the final surface of the parts.
The high sulfur content, added for machinability, is detrimental to hot workability. If hot forming is necessary, PRODEC® 304/304L or an intermediate sulfur level should be considered. When forging is necessary, it should be done in the 1800-2200°F range, and should be followed by annealing at 1900°F minimum and water quenching or rapid cooling by other means. The cold formability of PRODEC® 303 is limited by the sulfur content. Bending with a generous bend radius may be considered for PRODEC® 303. When cold forming is required, PRODEC® 304/304L should be considered.
PRODEC® 303 is not recommended for applications requiring welding. The high sulfur level in PRODEC® 303 makes it prone to weld solidification cracking. If welding is necessary, AWS E312 filler metal may be considered.
PRODEC® 303 is easily machined and produces small brittle chips. PRODEC® 303 may be machined at high speeds with deep cuts and heavy feeds on powerful, rigid equipment using good lubricants and sharp tooling.
Physical Properties
- Density: 0.285 lb/in³
- Modulus of Elasticity: 29 x 106 psi
- Linear Expansion 60-212 °F: 9.4 x 10-6/°F
- Thermal Conductivity: 8.7 Btu/ft hr °F
- Heat Capacity: 0.12 Btu/lb °F
- Electrical Resistivity: 27.6 O in x 10-6
Mechanical Properties
Typical Representative Tensile Properties
Tensile Strength, ksi | Yield Strength, ksi | % Elongation in 2 inches | % Reduction of area | Hardness, HB |
90 | 43 | 55 | 60 | 180 |
Machining Guidelines
High Speed Tooling | Carbide Tooling | ||||
Depth/Width, dia/in | Speed, sfm | Feed, in/rev | Speed, sfm | Feed, in/rev | |
Turning | 0.005 – 0.200 0.002- 0.004 | 115 -130 135 -180 | 0.015 – 0.020 0.005 – 0.010 | 375 -700 600 -900 | 0.025 – 0.030 0.007- 0.010 |
Cut-off | 1/16 1/4 | 90 -120 100 -130 | 0.0015 – 0.0020 0.0025 – 0.0030 | 275 – 400 325 – 450 | 0.002 – 0.004 0.004 – 0.008 |
Forming | 12 | 100 -130 90 -120 | 0.0020 0.0015 | 375 – 425 350 – 400 | 0.003 – 0.006 0.002- 0.004 |
Drilling | 1/4 1/2 1-2 | 70 – 80 85 -95 100 -110 | 0.007 0.012 0.020 | –7 00 800 | –0 .005 0.007 |
Reaming | 1/4 1-2 | 90 -110 90 -110 | 0.006 0.025 | – – | – – |
End Milling | 0.050 -1/2 0.050 -1/2 | 130 -160 130 -160 | 0.003 0.006 | 300 – 450 360 – 500 | 0.004 0.008 |
Tapping | 7 Threads/in | 10 -115 | – | – | – |
Threading | 25 Threads/in | 40 -50 | – | – | – |
PRODEC® 304/304L offers faster machining speeds, longer tool life, improved part quality and lower total cost of machined parts. PRODEC® 304/304L is nonmagnetic in the annealed condition, but may become slightly magnetic as a result of cold working or welding. PRODEC® 304/304L is a versatile, general purpose stainless steel with good resistance to atmospheric corrosion, to many organic and inorganic chemicals, as well as to food and beverages. It has also been used in vacuum processing equipment and specialized instruments where high integrity is essential.
Although improvements in machinability in the past have been associated with reduced corrosion resistance, PRODEC® 304/304L has been shown to have corrosion resistance within the range typically expected of 304L stainless steel. Because of its low carbon content, PRODEC® 304/304L retains this corrosion resistance in the as-welded condition.
It is common for PRODEC® 304/304L to be dual certified as both 304L and 304 when that material meets both the lower carbon limit of 304L and the slightly higher strength of 304. PRODEC® 304/304L is readily welded by full range of conventional welding procedures except oxyacetylene. AWS E308L/ER308L filler metal should be used with PRODEC® 304/304L steel.
Physical Properties
- Density: 0.285 lb/in³
- Modulus of Elasticity: 29 x 106 psi
- Linear Expansion 60-212 °F: 9.4 x 10-6/°F
- Thermal Conductivity: 8.7 Btu/ft hr °F
- Heat Capacity: 0.12 Btu/lb °F
- Electrical Resistivity: 27.6 O in x 10-6
Mechanical Properties
Typical Representative Tensile Properties
Tensile Strength, ksi | Yield Strength, ksi | % Elongation in 2 inches | % Reduction of area | Hardness, HB |
85 | 35 | 60 | 70 | 160 |
Minimum Tensile Properties ASTM A 276
Tensile Strength, ksi | Yield Strength, ksi | % Elongation in 2 inches | % Reduction of area | Hardness, HB |
75 | 30 | 40 | – | 201 |
PRODEC® 316/316L offers faster machining speeds, longer tool life, improved part quality and lower total cost of machined parts. PRODEC® 316/316L provides improved resistance over PRODEC® 304/304L to pitting and crevice corrosion in environments containing chlorides and other halides.
Although improvements in machinability in the past have been associated with reduced corrosion resistance, PRODEC® 316/316L has shown corrosion resistance within the range typically expected of 316L stainless steel. It is common for PRODEC® 316/316L to be dual certified as both 316L and 316. The material meets both the lower carbon limit of 316L and the slightly higher strength of 316.
PRODEC® 316/316L is readily welded by a full range of conventional welding procedures except oxyacetylene. AWS E316L/ER316L and other low carbon filler metals with molybdenum content higher than that of the base metal should be used with PRODEC® 316/316L stainless steel.
Physical Properties
- Density: 0.285 lb/in³
- Modulus of Elasticity: 29 x 106 psi
- Linear Expansion 60-212 °F: 9.4 x 10-6/°F
- Thermal Conductivity: 8.7 Btu/ft hr °F
- Heat Capacity: 0.12 Btu/lb °F
- Electrical Resistivity: 27.6 O in x 10-6
Mechanical Properties
Typical Representative Tensile Properties
Tensile Strength, ksi | Yield Strength, ksi | % Elongation in 2 inches | % Reduction of area | Hardness, HB |
85 | 44 | 56 | 69 | 170 |
Minimum Tensile Properties ASTM A 276
Tensile Strength, ksi | Yield Strength, ksi | % Elongation in 2 inches | % Reduction of area | Hardness, HB |
75 | 30 | 40 | – | 217 |
PRODEC® 17-4 is a newly developed enhanced machining version of 17-4 stainless PH. Trials have shown PRODEC® 17-4 to provide up to 30% faster machining speeds without sacrificing tool life when compared to standard 17-4. This enhanced machinability is a result of the PRODEC® melting process which reduces the quantity, size, and distribution of hard oxide inclusions. As a result, improved machining properties are realized in all heat treated conditions (Condition A, H1150, H1025, etc.) PRODEC® 17-4 round bar is produced in diameters ranging from 9/16″ to 6-1/2″.
17-4 is also commonly referred to as type 630 stainless. It is a martensitic, precipitation hardening stainless steel. A low temperature heat treatment can provide unusually high strength and hardness, with corrosion resistance similar to that of Type 304 austenitic stainless steel.
Physical Properties
- Density: 0.282 lb/in³
- Melting Range: 2560-2625°F
- Poisson’s Ratio: 0.272
- Electrical Resistivity: 463 Ohm-circ mil/ft
Mechanical Properties
Typical Representative Tensile Properties
Condition | Tensile Strength, ksi | 0.2% Yield Strength, ksi | % Elongation in 2 inches | % Reduction of area | Hardness, Rc | Charpy V-Notch Impact Strength, ft lb. |
H900 | 198 | 183 | 15 | 52 | 44 | 16 |
H1025 | 168 | 162 | 16 | 58 | 38 | 40 |
H1075 | 164 | 148 | 17 | 59 | 36 | 46 |
H1150 | 144 | 126 | 20 | 60 | 33 | 55 |
H1150M | 123 | 87 | 22 | 66 | 29 | 110 |
H1150D | 150 | 110 | 20 | 60 | 29 | 50 |
PRODEC 303 is a fully resulfurized free-machining austenitic stainless steel melted and processed to maximize machinability. It should be considered for automatic screw machines where extensive machining is required. PRODEC 303 is nonmagnetic in the annealed condition, but may become slightly magnetic as a result of cold working.
PRODEC 303 is resistant to mildly corrosive atmospheres, but is inferior to 304 because of the high sulfur content. For optimum corrosion resistance, it is recommended that PRODEC 303 be chemically treated to remove sulfides from the final surface of the parts.
The high sulfur content, added for machinability, is detrimental to hot workability. If hot forming is necessary, PRODEC 304/304L or an intermediate sulfur level should be considered. When forging is necessary, it should be done in the 1800-2200°F range, and should be followed by annealing at 1900°F minimum and water quenching or rapid cooling by other means. The cold formability of PRODEC 303 is limited by the sulfur content. Bending with a generous bend radius may be considered for PRODEC 303. When cold forming is required, PRODEC 304/304L should be considered.
PRODEC 303 is not recommended for applications requiring welding. The high sulfur level in PRODEC 303 makes it prone to weld solidification cracking. If welding is necessary, AWS E312 filler metal may be considered.
PRODEC 303 is easily machined and produces small brittle chips. PRODEC 303 may be machined at high speeds with deep cuts and heavy feeds on powerful, rigid equipment using good lubricants and sharp tooling.
Physical Properties
- Density: 0.285 lb/in³
- Modulus of Elasticity: 29 x 106 psi
- Linear Expansion 60-212 °F: 9.4 x 10-6/°F
- Thermal Conductivity: 8.7 Btu/ft hr °F
- Heat Capacity: 0.12 Btu/lb °F
- Electrical Resistivity: 27.6 O in x 10-6
PRODEC 304/304L offers faster machining speeds, longer tool life, improved part quality and lower total cost of machined parts. PRODEC 304/304L is nonmagnetic in the annealed condition, but may become slightly magnetic as a result of cold working or welding. PRODEC 304/304L is a versatile, general purpose stainless steel with good resistance to atmospheric corrosion, to many organic and inorganic chemicals, as well as to food and beverages. It has also been used in vacuum processing equipment and specialized instruments where high integrity is essential.
Although improvements in machinability in the past have been associated with reduced corrosion resistance, PRODEC 304/304L has been shown to have corrosion resistance within the range typically expected of 304L stainless steel. Because of its low carbon content, PRODEC 304/304L retains this corrosion resistance in the as-welded condition.
It is common for PRODEC 304/304L to be dual certified as both 304L and 304 when that material meets both the lower carbon limit of 304L and the slightly higher strength of 304. PRODEC 304/304L is readily welded by full range of conventional welding procedures except oxyacetylene. AWS E308L/ER308L filler metal should be used with PRODEC 304/304L steel.
Physical Properties
- Density: 0.285 lb/in³
- Modulus of Elasticity: 29 x 106 psi
- Linear Expansion 60-212 °F: 9.4 x 10-6/°F
- Thermal Conductivity: 8.7 Btu/ft hr °F
- Heat Capacity: 0.12 Btu/lb °F
- Electrical Resistivity: 27.6 O in x 10-6
PRODEC 316/316L offers faster machining speeds, longer tool life, improved part quality and lower total cost of machined parts. PRODEC 316/316L provides improved resistance over PRODEC 304/304L to pitting and crevice corrosion in environments containing chlorides and other halides.
Although improvements in machinability in the past have been associated with reduced corrosion resistance, PRODEC 316/316L has shown corrosion resistance within the range typically expected of 316L stainless steel. It is common for PRODEC 316/316L to be dual certified as both 316L and 316. The material meets both the lower carbon limit of 316L and the slightly higher strength of 316.
PRODEC 316/316L is readily welded by a full range of conventional welding procedures except oxyacetylene. AWS E316L/ER316L and other low carbon filler metals with molybdenum content higher than that of the base metal should be used with PRODEC 316/316L stainless steel.
Physical Properties
- Density: 0.285 lb/in³
- Modulus of Elasticity: 29 x 106 psi
- Linear Expansion 60-212 °F: 9.4 x 10-6/°F
- Thermal Conductivity: 8.7 Btu/ft hr °F
- Heat Capacity: 0.12 Btu/lb °F
- Electrical Resistivity: 27.6 O in x 10-6
PRODEC 17-4 is a newly developed enhanced machining version of 17-4 stainless PH. Trials have shown PRODEC 17-4 to provide up to 30% faster machining speeds without sacrificing tool life when compared to standard 17-4. This enhanced machinability is a result of the PRODEC melting process which reduces the quantity, size, and distribution of hard oxide inclusions. As a result, improved machining properties are realized in all heat treated conditions (Condition A, H1150, H1025, etc.) PRODEC 17-4 round bar is produced in diameters ranging from 9/16″ to 6-1/2″.
17-4 is also commonly referred to as type 630 stainless. It is a martensitic, precipitation hardening stainless steel. A low temperature heat treatment can provide unusually high strength and hardness, with corrosion resistance similar to that of Type 304 austenitic stainless steel.
Physical Properties
- Density: 0.282 lb/in³
- Melting Range: 2560-2625°F
- Poisson’s Ratio: 0.272
- Electrical Resistivity: 463 Ohm-circ mil/ft