Welding Information
WELD WIRE SELECTOR
When dealing with specialty alloys, there can be unique welding combinations where guidance is not easily found. The Rolled Alloys Weld Wire Selector helps to take guesswork out of the equation by allowing you to select any two alloys and see which weld wire is preferred. This tool was created with welders and fabricators in mind to determine the best wire options for their specific alloys or applications.
FABRICATION MANUALS
TYPES OF WELDING
Gas Metal Arc Welding (GMAW)
Gas Metal Arc Welding (GMAW), also known as Metal Inert Gas (MIG) welding, is a versatile arc welding process characterized by its automated wire feed system and external shielding gas protection. This method utilizes a solid wire electrode, continuously fed through a welding gun, with common diameters ranging from 0.035″ to 0.062″. GMAW offers precise control over various welding parameters, including wire feed rate, voltage, amperage, and frequency, allowing for optimized weld quality across different applications. The process is notable for its efficiency, with wire typically supplied in 30 or 33 lb. spools for extended operation. GMAW’s combination of automation, adjustability, and consistent shielding makes it ideal for a wide range of industrial applications, offering high deposition rates and
Gas Tungsten Arc Welding (GTAW)
Gas Tungsten Arc Welding (GTAW), also known as Tungsten Inert Gas (TIG) welding, is a precision arc welding process utilizing a non-consumable tungsten electrode. It’s distinguished by its manual filler wire feed method, where the welder hand-feeds solid wire into the arc to form the weld pool. The process employs external shielding gas, supplied through the GTAW torch, to protect the weld from atmospheric contamination. GTAW filler wire typically comes in 36-inch straight lengths, packaged in 10 or 11 lb. tubes, with standard diameters ranging from .045″ to .125″. This method offers exceptional control over the weld, making it ideal for high-quality, precise welding tasks, particularly with thin materials or in situations requiring superior aesthetic finish. GTAW is widely used in aerospace, automotive, and other industries where weld quality and appearance are critical.
Shielded Metal Arc Welding (SMAW)
Shielded Metal Arc Welding (SMAW), commonly known as “stick welding,” is an arc welding process that utilizes flux-coated electrodes. These electrodes consist of a core filler metal rod surrounded by a coating of flux, which serves two primary functions: it generates shielding gas during the welding process and forms a protective slag layer that must be removed after welding. This process is versatile, allowing for effective welding in various positions and materials, making it suitable for outdoor applications and fieldwork.
Electrodes are typically packaged in 10-pound containers and require careful storage to maintain their effectiveness; they must be kept dry, often in heated boxes, to prevent moisture damage. The classification system for electrodes, such as E308L-15, provides essential information about their composition and usability. In this example, “E” stands for electrode, “308” indicates the alloy composition, “L” signifies low carbon content, and “-15” denotes the coating type suitable for direct current positive polarity.
The coating plays a crucial role in determining the electrode’s usability, polarity, and overall welding characteristics. It influences arc stability and weld quality while generating shielding gas to protect the weld pool from contamination. Below is a table that provides information on common stainless steel and nickel alloy SMAW electrode coatings and their welding characteristics.
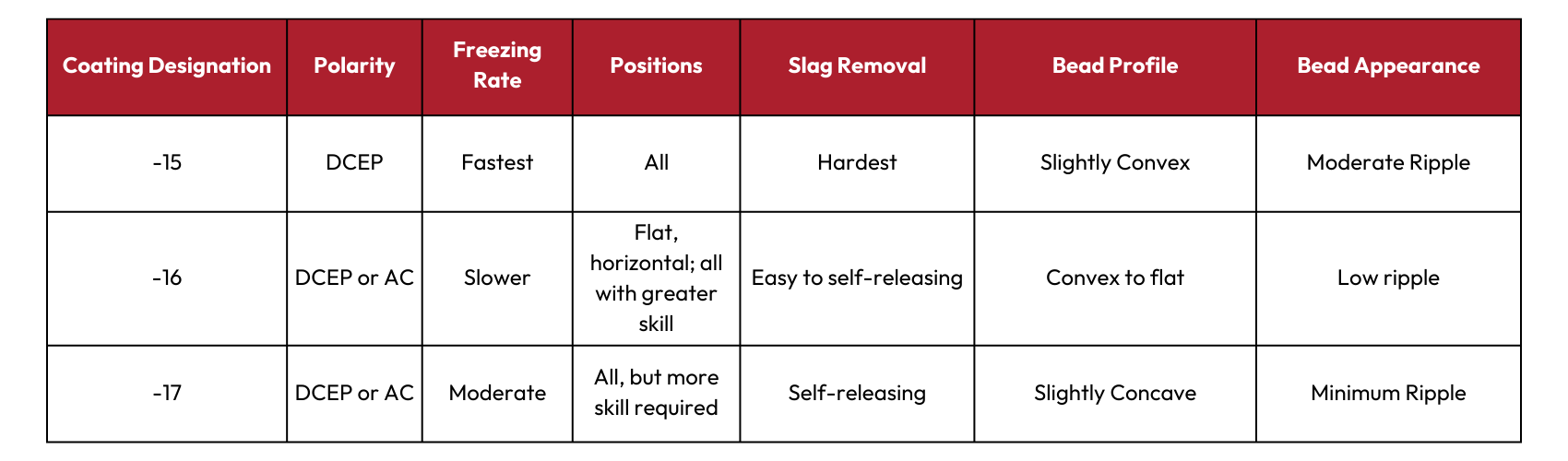
Flux Cored Arc Welding (FCAW)
Flux Cored Arc Welding (FCAW) is an advanced arc welding process that combines elements of GMAW (Gas Metal Arc Welding) and SMAW (Shielded Metal Arc Welding). It utilizes a unique tubular wire electrode filled with powdered flux, offering superior weld quality and efficiency. The process involves automatic wire feeding through a welding gun, similar to GMAW, but with added benefits from the flux core. This flux serves multiple purposes: it generates a protective gas shield, forms a slag covering that protects the weld from atmospheric contamination, and can introduce alloying elements to enhance weld properties. FCAW is versatile, in that it can be done both with gas-shielding and self-shielding, making it suitable for various applications, including outdoor welding. The process is particularly effective with stainless steel and nickel-grade alloys, offering high deposition rates and excellent weld quality.
WELDING POSITIONS
Understanding weld positions is essential for achieving high-quality and safe welds. The four primary welding positions—flat (1G/1F), horizontal (2G/2F), vertical (3G/3F), and overhead (4G/4F)—each present unique challenges that can significantly affect the welding process.
In flat position welding, the workpiece is positioned horizontally, allowing for optimal visibility and control over the weld puddle, making it the easiest position for welders. As we move to horizontal and vertical positions, the difficulty increases due to the influence of gravity on the molten metal, requiring greater skill to maintain a consistent weld. Overhead welding is often viewed as the most challenging position, as it demands precise technique to prevent weld metal from dripping and ensure a strong bond.
Additionally, specialized positions such as 5G and 6G are used primarily in pipe welding, with 6G being particularly complex due to its fixed angle that requires welders to work around the entire circumference of the pipe. Understanding these positions not only enhances a welder’s skill set but also ensures that they can tackle a wide range of projects effectively.
SCHAEFFLER-DELONG DIAGRAM
The Schaeffler-DeLong diagram is a graphical tool used to predict the microstructure of stainless-steel welds based on their chemical composition. It plots the nickel equivalent against the chromium equivalent, which represent the austenite-forming and ferrite-forming elements, respectively. This diagram is crucial in welding stainless steel as it helps engineers and welders anticipate the final weld structure, including the balance of austenite, ferrite, and martensite.
The importance of the Schaeffler-DeLong diagram in stainless steel welding lies in its ability to forecast potential issues and optimize weld properties. By predicting the microstructure, welders can avoid problems such as hot cracking, which is more likely in fully austenitic structures, or excessive ferrite formation, which can lead to reduced corrosion resistance. Additionally, the diagram aids in selecting appropriate filler metals and welding parameters to achieve the desired weld characteristics.
Consideration of the Schaeffler-DeLong diagram is essential for ensuring weld quality and performance in stainless steel applications. It allows for the fine-tuning of weld compositions to balance strength, ductility, and corrosion resistance. Furthermore, the diagram helps in understanding the effects of dilution when welding dissimilar metals, enabling welders to make informed decisions about joint design and welding techniques. By utilizing this tool, manufacturers can optimize their welding processes, leading to improved product reliability and longevity in various industries, including nuclear, chemical, and aerospace sectors.
Do you have a question about a weld wire selection?
Share This Page